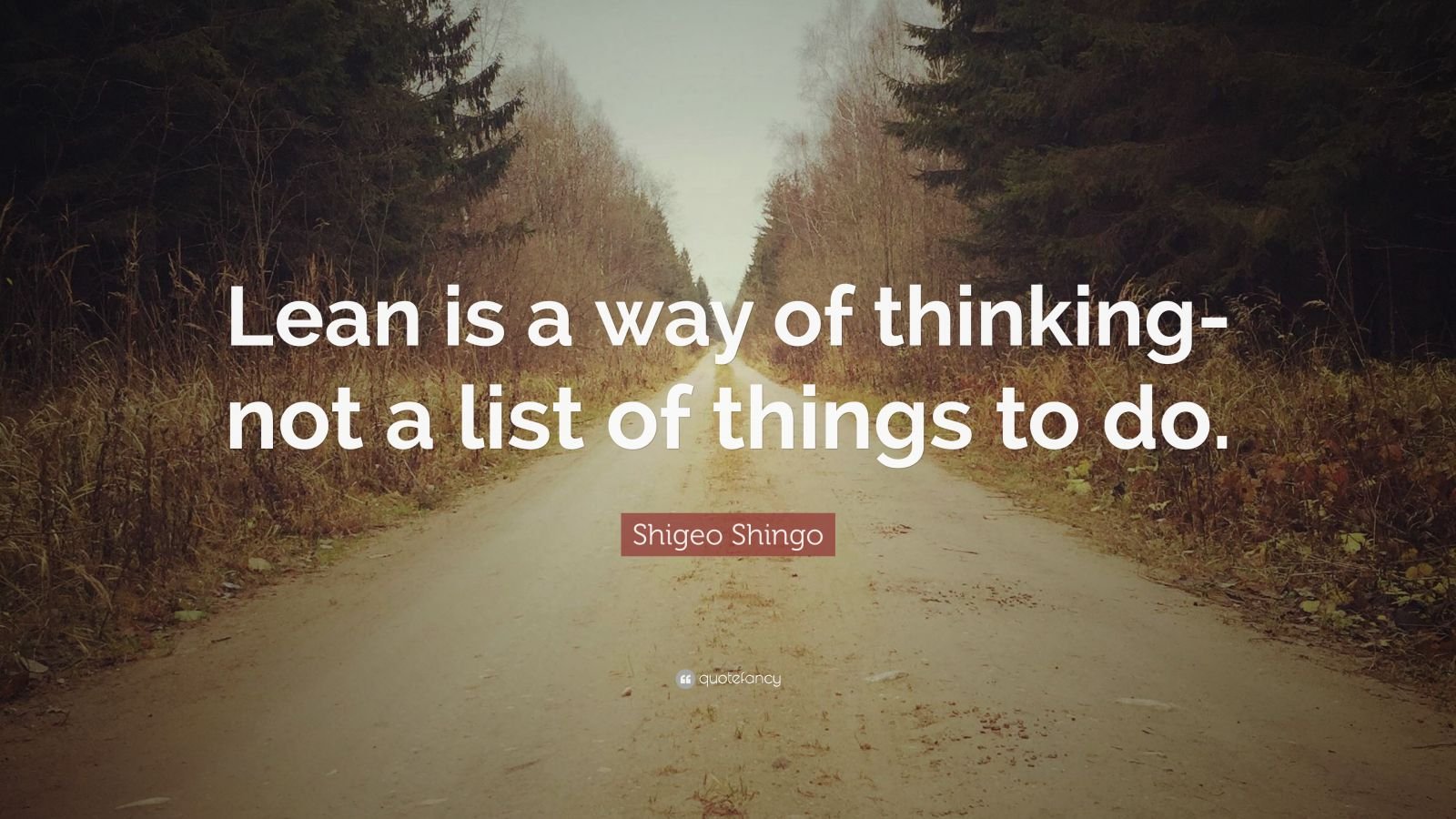
Notable Case Studies
ALL CASE STUDIES AND NUMBERS THROUGHOUT ARE GENERALIZED IN ORDER TO PROTECT THE CONFIDENTIALITY OF THE COMPANIES
PROBLEM: Several hundred thousand escalations from frontline experts to technical leads during peak season, averaging 31 minutes for resolution and totaling tens of millions in overhead costs.
METHODS: Value Stream Mapping (VSM), Kaizen, AI, Robotic Process Automation (RPA), Standard Work
RESULT: 19% reduction in escalation resolution time and 16% reduction in overall escalations, resulting in savings of $14.5 million.
PROBLEM: The company had several months of product backlog, averaging two weeks of additional backlog each quarter, with a goal of reducing the backlog to one month or less.
METHODS: Hoshin Kanri (Strategy Deployment), Value Stream Mapping (VSM), Kaizen, Daily Management, Leader Standard Work (LSW), Standard Work
RESULT: The reduction of three months in product backlog, with an additional average decrease in product backlog of two weeks each quarter.
PROBLEM: The goal for time to effectiveness—when an employee feels oriented and impactful after being onboarded—is 30 days. The company was at 93 days and had been trending upwards by more than 5 days each year for the past four years, resulting in increased attrition.
METHODS: Net Promoter Score (NPS), Process Mapping, Standard Work, Lean Leadership
RESULT: Time to effectiveness reduced from 93 to 34 days, with a 10% increase in employee engagement and a 3% reduction in attrition.
Case Studies by Industry
AUTOMOTIVE
PROBLEM: Shift handovers were conducted with incomplete information and high variability, resulting in unfinished tasks, misaligned priorities, and inefficiencies.
METHODS: Daily Management, Standard Work, Leader Standard Work
RESULT: There was a 15% increase in productivity on the pilot line when implemented, which resulted in a 12% productivity increase when scaled to the entire plant.
MEDICAL
PROBLEM: The lack of visibility for over 500 pieces of equipment, along with poor management of calibration logs, resulted in an Overall Equipment Efficiency (OEE) of 23%, putting the company's contracts at risk due to quality issues.
METHODS: Computerized Maintenance Management System (CMMS), Daily Management, Leader Standard Work
RESULT: All equipment is now fully maintained and calibrated with a robust scheduling system, which has led to over 90% OEE.
ENERGY
PROBLEM: Airflow across heatshields was highly variable at over 50%, which led to hot spots and lower unit efficiency.
METHODS: Six Sigma, Standard Work
RESULT: Lowered variability to within 3% of each measuring point and increased efficiency of units by 15% overall.
TECHNOLOGY
PROBLEM: The company was incurring millions in consumable expenses annually without visibility into inventory levels, associated costs, or an effective management system. This lack of oversight led to inefficiencies, waste, and missed opportunities for cost control and optimization
METHODS: Kanban, Standard Work, 5S
RESULT: Implementing 5S, Kanban, and standard work-optimized consumable management by organizing inventory, streamlining replenishment, and standardizing processes, resulting in reduced waste and reduced budget by 50%.
GOVERNMENT CONTRACTS
PROBLEM: Sitewide training was delinquent across hundreds of employees, including mandatory compliance training, which left the company at risk.
METHODS: Kirkpatrick Training Method, Training Program, Facilitation, Train-the-Trainer, Daily Management, Leader Standard Work, Standard Work
RESULT: A comprehensive training program utilizing an online learning system for improved tracking and visibility was implemented, which resulted in zero delinquencies and a top-tier site training program.
AEROSPACE
PROBLEM: The company struggled to adopt a Lean operating model due to inadequate change management, a resistant culture, and limited leadership support, resulting in stalled initiatives, low engagement, and missed improvement opportunities.
METHODS: Organizational Design, Change Management, Lean Leadership
RESULT: The company successfully adopted a Lean operating model by prioritizing effective change management and fostering a culture of continuous improvement. This alignment drove employee engagement and sustained process improvements.